Material Selection
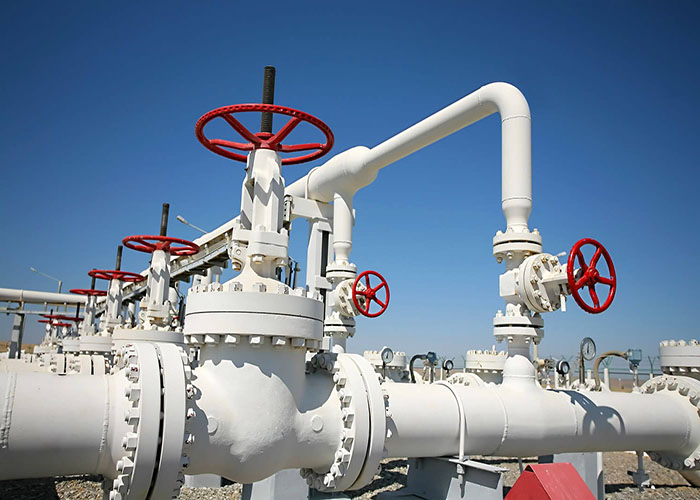
Material Selection
Key factors considered are:
- Market Availability and proven fabrication and service providers
- Life cycle costing.
- Design life.
- Operating conditions.
- Process requirements.
- Experience with materials and corrosion protection methods from conditions with similar corrosivity.
- Philosophy applied for maintenance and degree of system redundancy.
- In-service Inspection and corrosion monitoring possibilities.
- Effect of external and internal environment, including compatibility of different materials.
- Evaluation of failure probabilities, failure modes, criticalities, and consequences.
- Environmental issues related to corrosion inhibition and other chemical treatments.
A material selection report comprises of
Material Selection Diagrams (MSDs): These are schematic representations that show the type of materials used in different parts of a system or facility, such as a pipeline, processing unit, or entire plant. MSDs typically include information on the specific materials chosen for each component and may also indicate the operating conditions (like temperature and pressure) that the materials are expected to withstand. They serve as a quick reference for engineers and technicians and are crucial for maintenance and inspection planning.
Marking of Corrosion Loops: This involves identifying and documenting different sections of a system or facility that are expected to experience similar corrosion mechanisms and rates. Each corrosion loop is evaluated based on factors like the presence of corrosive agents, temperature, pressure, and flow dynamics. By marking these loops, engineers can more effectively monitor and manage corrosion risks, tailoring inspection and maintenance activities to the specific needs of each loop.
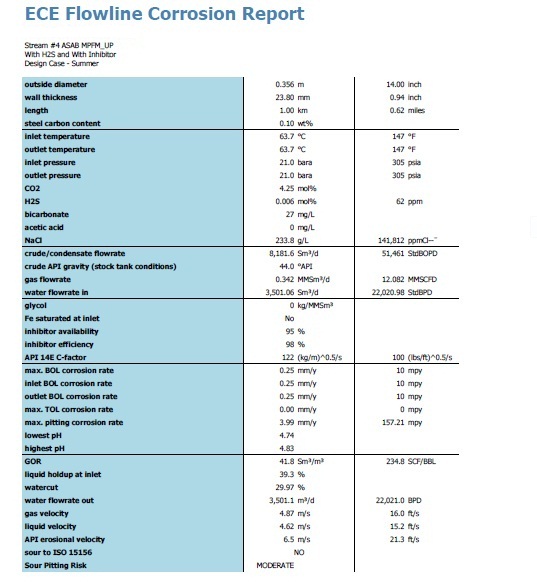