Corrosion Under Insulation (CUI) at a Dubai Hotel Swimming Pool
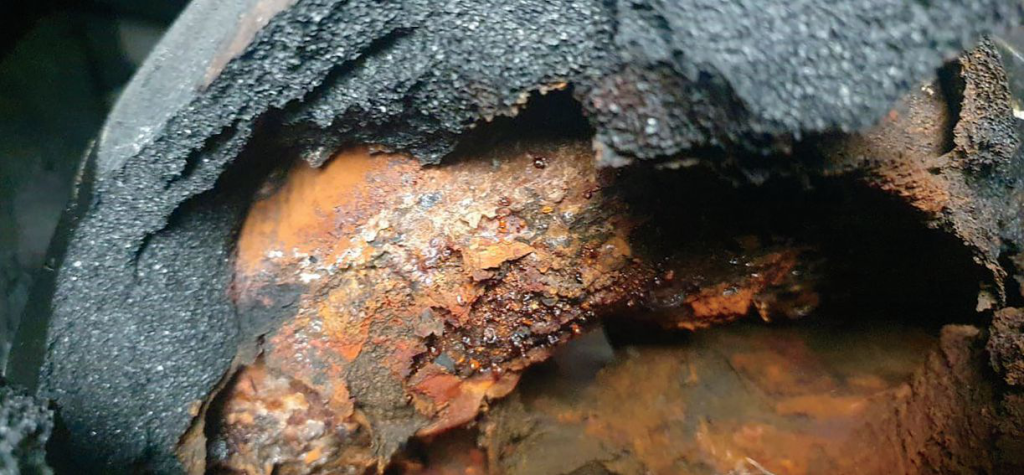
Introduction
This case study examines a severe corrosion incident in a chilled water system at a hotel in Dubai. The system, serving air handling units (AHUs) and swimming pools, experienced significant external corrosion within three years of installation. This case underscores the critical importance of proper design, material selection, installation, and maintenance in preventing Corrosion Under Insulation (CUI). The study includes detailed technical specifications and testing results.
Background
- System:Chilled water application system.
- Operating Conditions:
- Pressure: < 10 bars (145.0 psi)
- Temperature: 65 to 80 °C (149.0 to 176.0 °F)
- Materials:
- Piping:2-inch (5.1 cm) Schedule 40 Grade B ERW black steel pipe per ASTM A53.
- Internal Coating:Specified epoxy coating (application inadequately met).
- External Coating System (Specified):
- First Layer: Epicon Zinc Rich Primer B-2 + thinner (or equivalent), 75 microns (3.0 mils) DFT.
- Second Layer: Epicon HB-CL + thinner (or equivalent), 50 microns (2.0 mils) DFT.
- Third Layer: UNY Marine 100 + thinner (or equivalent), 50 microns (2.0 mils) DFT.
- Insulation:Closed-cell nitrile butadiene rubber (NBR) elastomeric foam.
- Field Insulation:Specified to meet “Sheet Metal Ducts Thermal Insulation Wrap Commercial/Residential Duct Systems” requirements per UAE jurisdiction (reference to Section 15082 was made).
- History:System in operation for almost two years under a maintenance contract before handover. First leak reported August 2019; multiple leaks led to closure in March 2020.
Problem Description
Significant external corrosion was observed. Visual inspection revealed:
- Extensive corrosion evident at joint locations, characterized by rough, pitted surfaces with loose, flaky scale.
- Severe corrosion at tube-to-coupler joints and elbows.
- External Coating Thickness:Actual thicknesses of 106-152 microns (4.2-6.0 mils) at “normal” locations, falling below project specification requirements (which called for a combined 175 microns).
- Minimal internal corrosion, but significant crevice corrosion on the coupler threads.
- Evidence of external insulation failure (as seen in Figure 1 of the article), which allowed moisture ingress.
Investigation & Testing Methods
A corrosion specialist conducted a site visit and performed the following tests:
- Visual Inspection:Documentation of corrosion’s extent and characteristics.
- Coating Thickness Measurement:Non-destructive measurements using a gauge to determine coating thickness.
- Chemical Analysis (OES):Optical Emission Spectroscopy using ASTM E415-17:
- Confirmed pipe material conformed to ASTM A53 Grade B requirements.
- Tensile Testing (ASTM A370-17a):Conducted to evaluate mechanical properties:
- Yield Strength, Tensile Strength, and Elongation met requirements of ASTM A53 Grade B (except for elongation which was not considered critical in the study).
- Hardness Testing (ASTM E92-17):Vickers Hardness Test.
- Hardness values ranged from 146 to 152 HV10 (with 10 kg load).
- Microstructure Analysis (ASTM E3-11/E407-07):
- Uniform distribution of ferrite and pearlite observed (as shown in Figure 4 of the article).
- X-Ray Diffraction (XRD):Identified constituents of corrosion scale:
- Magnetite (41.6%)
- Goethite (24.5%)
- Hematite (20.6%)
- Chalcopyrite (5.4%)
- Lepidocrocite (6.3%)
- Quartz (1.6%)
- Water Analysis (APHA 23rd Ed. Methods):
- pH: 8.40
- Total Dissolved Solids (TDS): 205.00 mg/L
- Electrical Conductivity: 354.14 µS/cm
- Chlorides (as Cl): 85.880 mg/L
- Sulphide: 0.02 mg/L
- Iron (Fe): 2.28 mg/L
- Dissolved Oxygen: 7.1 mg/L
- No signs of microbiological activity detected.
Findings & Technical Analysis
- Corrosion Mechanism:Primary corrosion mechanism identified as CUI.
- Coating Failure:Inconsistent and inadequate coating application resulted in under-protection of base metal.
- Moisture Ingress:Failure of the insulation and vapor barrier allowed moisture to reach the pipe surface.
- Crevice Corrosion:The design of the threaded pipe couplers allowed moisture to accumulate, exacerbating crevice corrosion.
- Water Chemistry:Although slightly alkaline, the water chemistry did not indicate any aggressive components that would significantly contribute to the corrosion of the materials used; therefore, it was determined that water exposure due to insulation failure was the primary issue.
Lessons Learned & Mitigation Strategies
- Coating Application:
- Implement strict quality control during coating application.
- Ensure consistent coating application in accordance with specification.
- Pay close attention to coating thickness, particularly at joints and irregular surfaces.
- Insulation System Design:
- Use a multi-layered insulation approach with an effective vapor barrier
- Design the insulation system to shed water effectively.
- Pay specific attention to joints and terminations.
- Material Selection:
- Consider selecting insulating materials that have low water absorption rates, and quick water evaporation rates.
- Use corrosion-resistant coatings such as flame-sprayed aluminium when applicable.
- Select insulation containing corrosion inhibitors.
- Maintenance:
- Implement regular inspections of insulation and protective coatings.
- Replace damaged or degraded insulation promptly.
- Address any signs of leaks or moisture intrusion immediately.
- Design Considerations:
- Minimize crevices and other water-trapping areas.
- Use appropriate pipe supports and hangers to ensure water can’t pool.
- Consider using open-cell insulation when appropriate.
Conclusion
This case study emphasizes the importance of a comprehensive approach to preventing CUI. This approach should include:
- Proper coating application.
- Careful insulation selection, design, and installation.
- Regular inspections and maintenance, including immediate response to issues.
The technical data obtained in this investigation provides a detailed example of the corrosion mechanism, and helps engineers understand the complexities and risks associated with CUI. By taking the lessons learned from this event, future corrosion incidents can be mitigated, reducing costs, increasing system reliability, and ensuring the long-term integrity of insulated systems.