Coating Deterioration Assessment of a High-Rise Steel Structure in Baku
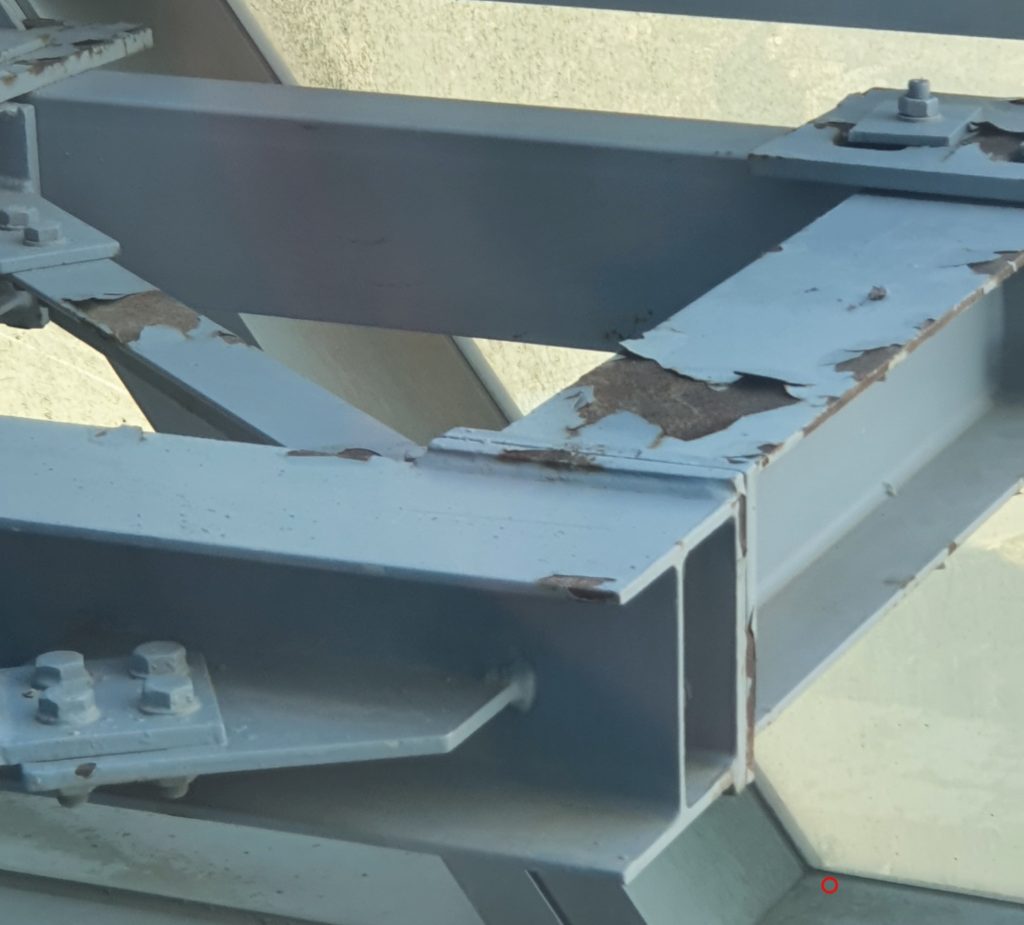
Background
In 2013, XXXX, a prominent construction company, was awarded the contract for the prestigious steel structure project in Baku, Azerbaijan. The structural steel painting contract was awarded to a contractor based in the UAE, who commenced painting in March 2014 and completed the installation by July 2014. However, approximately four years after the project’s completion, significant coating deterioration was observed, including cracking and delamination of the paint on the steel structure.
XXXX approached Colossal Consultants in December 2020 to conduct a detailed investigation to determine the root cause of the coating deterioration and provide recommendations for remediation.
Scope of Work
Colossal Consultants proposed a comprehensive scope of work to investigate the coating deterioration, which included:
- Document Review: Examination of painting procedures, paint application reports, and technical specifications.
- Site Testing:
- Visual examination of the coating condition.
- Coating thickness verification using random sampling.
- Adhesion testing on existing coatings.
- Salt contamination testing.
- Determination of the corrosivity category for the Baku region.
- Laboratory Testing:
- Salt spray and condensation tests on panels prepared by the paint manufacturer.
- Fourier-transform infrared spectroscopy (FTIR) analysis of coating samples to evaluate chemical composition.
Findings
- Document Review
The painting system used for the project consisted of:
- Primer: Hempadur Zinc 17360 (40 microns)
- Intermediate Coat: Hempadur Fast Dry 17410 (70 microns)
- Finish Coat: Hempathane HS 55610 (50 microns)
The total dry film thickness (DFT) was specified at 160 microns, designed for a C3 Corrosivity High Durability environment as per ISO 12944. However, the contractor failed to provide detailed inspection reports for each stage of the coating process, raising concerns about the quality control during application.
- Site Testing
- Visual Examination: Extensive cracking and peeling of the coating were observed, particularly at sharp edges and corners of the structural steel. The design of the structure lacked proper drainage, leading to water accumulation in certain areas, which exacerbated the coating deterioration.
- Coating Thickness (DFT) Verification: The average DFT was found to be 238 microns in March 2021, exceeding the specified 160 microns. While higher DFT can provide better protection, excessive thickness can lead to internal stresses and cracking, especially at sharp edges.
- Adhesion Testing: The adhesion values were satisfactory, with an average of 8 MPa. However, the high adhesion values near cracked areas indicated a lack of flexibility in the coating, contributing to the cracking.
- Salt Contamination Test: The maximum salt contamination value recorded was 2.7 µg/cm², well below the acceptable limit of 5 µg/cm² as per ISO/TR 15235. This ruled out salt contamination as a contributing factor to the coating failure.
- Corrosivity Category for Baku: Based on ISO 9223, the corrosivity category for Baku was determined to be C3, which aligns with the paint system’s design specifications.
- Laboratory Testing
- Salt Spray and Condensation Tests: The paint system was tested in the laboratory and found to comply with the C3 High Durability requirements as per ISO 12944. The panels showed no signs of blistering, chalking, or discoloration after 480 hours of salt spray testing and 240 hours of condensation testing.
- FTIR Analysis: The FTIR analysis revealed that the primer and intermediate coats had lower epoxy content than expected, indicating improper mixing of the base and hardener. This improper mixing led to a lack of flexibility in the coating, resulting in cracking and delamination.
Conclusions
The coating deterioration was primarily attributed to improper application by the contractor, specifically:
- Incorrect Mixing Ratio: The primer and intermediate coats had lower epoxy content than specified, leading to a lack of flexibility and increased internal stresses within the coating system.
- Sharp Edges and Poor Drainage: The structural design did not account for proper drainage, leading to water accumulation. Additionally, sharp edges were not rounded off, creating stress points that contributed to coating failure.
- Lack of Documentation: The contractor failed to provide detailed inspection reports, raising doubts about the quality control during the painting process.
The corrosion problem was not due to external environmental factors but rather the result of negligence during the application process.
Recommendations
- Coating Rehabilitation: All areas showing coating deterioration should be rehabilitated. Proper surface preparation, correct mixing ratios, and adherence to application procedures must be ensured.
- Rounding Off Sharp Edges: Sharp edges on the structural steel should be rounded off to prevent stress concentration and subsequent coating failure.
- Drainage Improvements: Drainage holes should be added to prevent water accumulation, which can lead to localized coating holidays and microbiological activity.
- Quality Control: Future projects should include rigorous quality control measures, including detailed documentation of each stage of the coating process.