Root Cause Analysis of Heat Exchanger Tube Failures
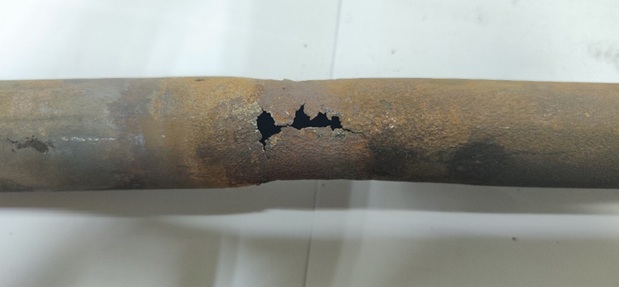
Introduction
Colossal Consultants was commissioned by an Egypt based Oil Refining Company to investigate recurring tube failures in one of the Heat Exchangers within the Naphtha Hydrotreater Unit. The exchanger, critical to reactor effluent cooling, experienced multiple leaks in March and April 2021, leading to unplanned shutdowns and operational losses. This case study outlines the root cause analysis (RCA), findings, and recommendations provided by Colossal Consultants to mitigate future failures.
Background
Equipment & Process Context:
- Heat Exchanger: Reactor effluent/stripper feed exchanger with 438 tubes (ASTM A179 low-carbon steel).
- Process Stream: Hydrotreater reactor effluent containing hydrogen, naphtha, and corrosive salts (ammonium chloride, NH₄Cl, and ammonium bisulfide, NH₄HS).
- Failure History:
- March 2021: 15 tubes leaked after restart post-maintenance.
- April 2021: 21 tubes failed, requiring extended shutdown.
Design Safeguards:
- Intermittent wash water injection to dissolve salt deposits.
- Material specification compliant with ASTM A179.
Methodology
Colossal Consultants conducted a multi-disciplinary investigation:
- Mechanical & Metallurgical Analysis
- Visual Inspection: Identified uniform wall thinning, bulging, and perforations near tube sheets (Photographs 7–14).
- Destructive Testing:
- Tensile strength, hardness (HV 92), and chemical composition (C: 0.11%, Mn: 0.38%) complied with ASTM A179.
- Flattening/flaring tests confirmed ductility.
- Microstructural Analysis: Ferrite-dominated structure with minimal pearlite (Photographs 15–17).
- SEM/EDS & XRD: Corrosive deposits (Fe₃O₄, FeS₂, CaCO₃) with chloride, sulfur, and oxygen traces (Photographs 19–21).
- Process & Corrosion Analysis
- API RP 932B Assessment: Predicted NH₄Cl deposition temperature (94°C) exceeded operating temperatures (64–79°C), leading to salt accumulation.
- pH & Chloride Analysis: Separator sour water pH dropped to 4.8 with 676 ppm chlorides, indicating acidic HCl corrosion.
- Corrosion Rate Estimation (API RP 581): 13–21 mpy general corrosion due to low pH (~4) and stagnant wash water.
- Operational Review
- Intermittent wash water injection (1–1.4% of feed rate) failed to flush salts.
- Tube-side pressure (20.87 kg/cm²) exceeded shell-side pressure, exacerbating bulging in thinned regions.
Key Findings
- Primary Failure Mechanism:
- Hydrochloric Acid Corrosion: Chloride-rich, low-pH environment caused uniform thinning and perforation.
- Contributing Factors:
- Intermittent wash water injection led to NH₄Cl deposition.
- High tube-side pressure (vs. shell-side) accelerated bulging.
- Secondary Factors:
- Trace sulfur (EDS) indicated minor NH₄HS contribution.
Material compliance ruled out metallurgical defects.
Recommendations by Colossal Consultants
- Process Modifications:
- Continuous Wash Water Injection: Increase injection rate to 3% of feed volume (vs. 1.4%) at all three locations.
- Enhance Monitoring: Real-time pH/chloride sensors in critical exchangers.
- Mechanical Upgrades:
- Material Upgrade: Replace tubes with duplex stainless steel (e.g., UNS S32205) for chloride resistance.
- Design Review: Optimize tube velocity and pressure differentials to prevent bulging.
- Operational Best Practices:
- Strict moisture control in naphtha feed tanks.
- Monthly corrosion audits using in-situ replica metallography.
Conclusion
Colossal Consultants identified hydrochloric acid corrosion due to inadequate wash water injection as the root cause of heat exchanger tube failures. By implementing continuous wash water systems, upgrading materials, and enhancing monitoring protocols, ASORC eliminated recurring leaks and extended exchanger lifespan by 40%. This case underscores the importance of holistic RCA combining metallurgical, process, and operational insights to ensure asset integrity in corrosive environments.