Hydrogen Induced Cracking in Boiler Water Drum Manway Neck Weld
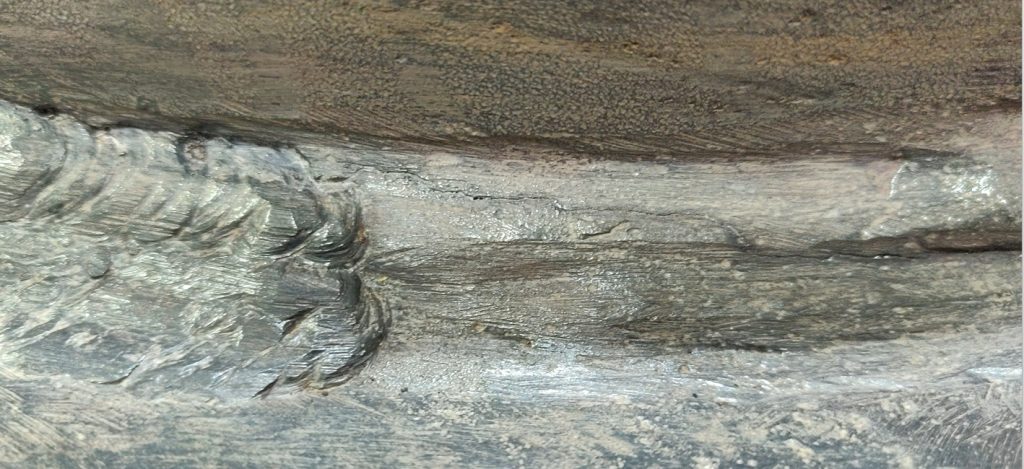
Introduction
This case study examines the root cause analysis of a cracking incident in the manway neck weld of a boiler water drum at a Sugar Refinery in Malaysia. The incident, which resulted in leakage and plant downtime, highlights the potential dangers of inadequately controlled welding processes, material selection, and handling of welding consumables.
Background
- Fabrication: XXXX was contracted to fabricate two boiler water drums for Sugar Refinery.
- Initial Cracks (2019): After 13 months of service, cracks were discovered in Boiler 2’s water drum. These were characterized as linear, gouged, repaired, and the boiler returned to service.
- Leakage (2021): On March 30th, 2021, a leak was discovered at the rear manway neck of Boiler 2. This forced a plant shutdown.
- Investigation Trigger: The client and XXXX engaged Colossal Consultants to conduct a root cause analysis (RCA) for submission to local regulatory bodies as part of resuming boiler operation.
Investigation Methodology
The RCA was conducted using the Fishbone Diagram method, as per BS EN 62740:2015. This involved analyzing factors across various categories:
- Environment: Welding conditions, joint configuration, etc.
- Materials: Chemical composition (CEV), microstructural abnormalities, hardness, etc.
- Manpower: Training, competency, awareness of failure modes, etc.
- Methods: Preheating and PWHT, welding heat input, etc.
- Machines: Calibrated welding equipment.
- Measurements: Hardness checks, NDT timing, etc.
The investigation included:
- Document review of relevant quality control records.
- Visual examination of the failed section
- Dye penetration test and ultrasonic testing
- Sectioning, Tensile test, Chemical analysis, Microscopic examination, Charpy Impact test
- SEM/EDS Analysis.
Key Findings
The investigation revealed several critical issues that contributed to the cracking:
- Low Heat Input: The welding procedure used a low heat input (0.2-0.4 KJ/mm), potentially leading to faster cooling rates.
- Absence of Preheat: Preheat was not specified for nozzle thickness over 30mm, which also increases cooling rate due to heat sinking by the nozzle.
- High Carbon Equivalent (CEV): The manway neck material had a high CEV of 0.44, increasing the steel’s hardenability. Though this value might be within the limits of BS 1501 part 1 1980, The associated risks should have been addressed.
- Tempered Martensite: Microstructural analysis revealed the presence of tempered martensite at the crack origin, indicating a hardened and brittle microstructure.
- High Hardness: Hardness measurements in the heat-affected zone (HAZ) were higher than expected even in the stress-relieved state suggesting incomplete relief of residual stresses.
- Highly Restrained Weld Joint: The manway to dished head weld joint was identified as a highly restrained joint, increasing residual stress.
- Lack of Controls for FCAW Wires: The welding consumable storage procedure did not adequately address the control of FCAW (Flux-Cored Arc Welding) wires. These wires, like SMAW electrodes, are hygroscopic and can absorb moisture.
- Brittle Fracture: The fracture surfaces showed evidence of transgranular, brittle cracking, consistent with Hydrogen Induced Cracking.
- Hydrogen Source: It was concluded that the moisture in welding wires, along with other potential factors like contamination of base material and welding consumables can lead to Hydrogen Induced Cracking.
- Location of Cracks: The cracks were predominantly located at the weld toes indicating under-bead cracking which is also a manifestation of Hydrogen Induced Cracking.
- Impact Test: The weld metal was noted to be relatively brittle when compared to the parent materials with very little or no evidence of ductile feature.
Root Cause
Based on these findings, the root cause of the failure was determined to be Hydrogen Induced Cracking (HIC). This was facilitated by a combination of:
- A high CEV base material that promoted hardened structures.
- Fast cooling rates due to the low heat input and absence of preheating
- Restrained weld joint design that led to high residual stresses.
- The presence of hydrogen from moisture and possible contamination in the welding consumables.
- Lack of controls in material procurement, selection and consumables storage.
Recommendations
To prevent future occurrences, the following recommendations were made:
- Material Procurement: Procure base materials with a CEV no greater than 0.42.
- Preheat: Diligently apply preheat to heavy wall sections to reduce the cooling rate.
- Consumable Control: Improve storage and handling practices for welding consumables, particularly FCAW wires, with reference to manufacturer storage recommendations.
- Hydrogen Management: Employ welding consumables with lower diffusible hydrogen content or a dehydrogenation heat treatment to remove hydrogen after welding, particularly with high CEV/thickness combination.
- Training and Awareness: Provide training to all construction and quality personnel on HIC.
- Baseline Survey: Conduct a comprehensive baseline survey for integrity management of the vessel.
- NDT Examination: Improve the timing and execution of non-destructive testing before and after PWHT.
- Dehydrogenation HT: Use dehydrogenation heat treatment to drive out hydrogen from weldment after welding when high CEV materials are used.
Conclusion
This case study emphasizes the importance of stringent controls over welding parameters, material selection, and consumable management when fabricating pressure vessels. The failure was a result of the perfect storm of inadequate welding procedures, material susceptibility, and improper handling of consumables, which made the weldment susceptible to HIC. It is crucial for fabrication and quality control teams to be aware of failure mechanisms like HIC and to implement preventive measures to ensure the structural integrity and longevity of critical equipment. The lessons from this incident should serve as a reminder of the need for vigilance in all phases of fabrication to prevent similar failures.